Room to Breathe red stencil typography

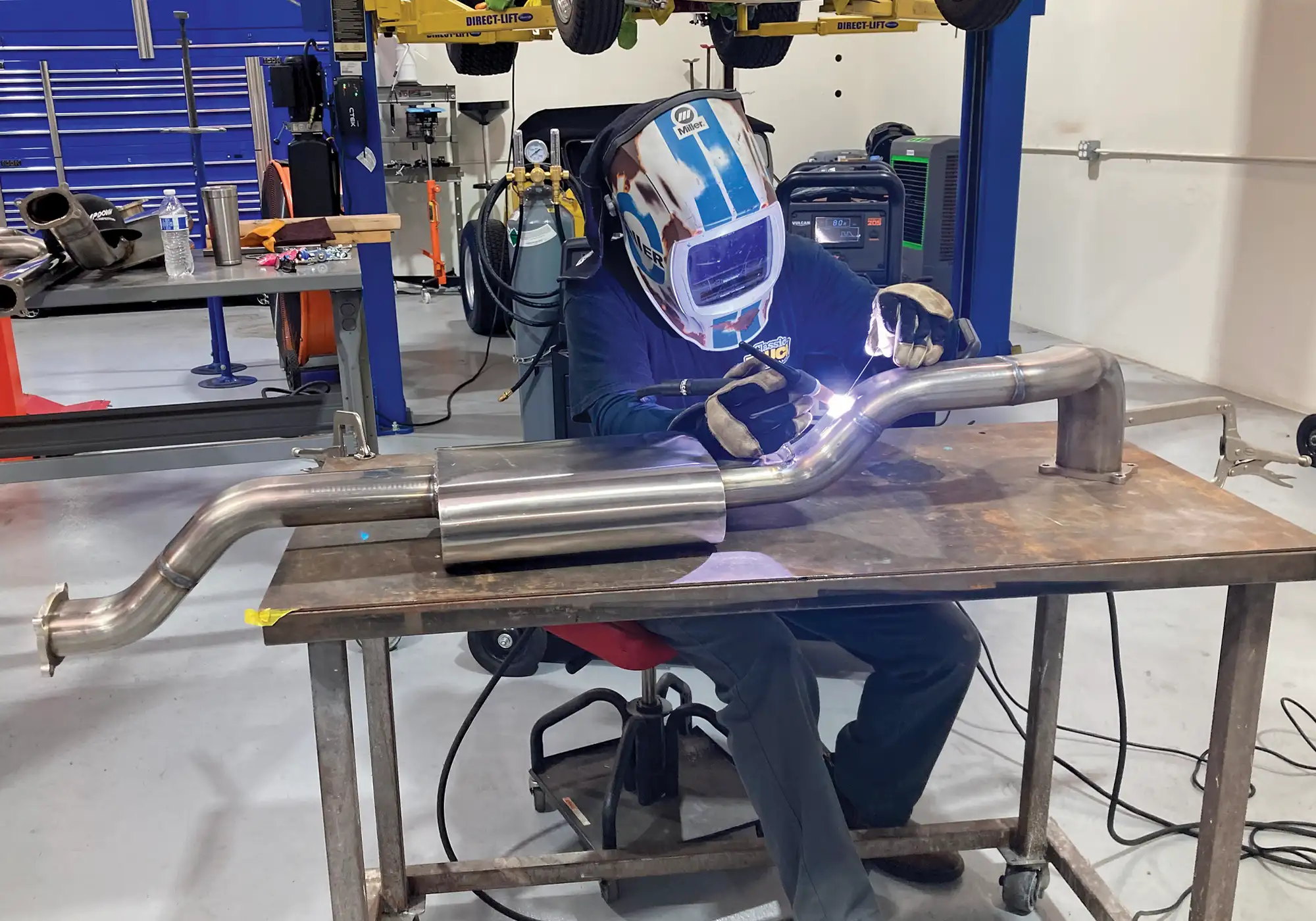

hen it comes time to tackle the exhaust system of your classic truck build, you’ll no doubt be presented a handful of options. In the past, most simply took their truck down to the local muffler shop for a traditional dual exhaust install. Today, a myriad of bolt-on exhaust kits can be ordered for some of the more popular models and engine configurations, making it possible for the DIYer to exhaust themselves in the comfort of their own home. For the ultimate custom applications, however, a fully fabricated stainless steel exhaust is the pinnacle of both performance and aesthetic.
After plumbing the chassis of our project 1964 Chevy C10, we turned our attention to the exhaust, or lack thereof. We thought briefly about purchasing an over-the-counter, bolt-on kit, but quickly realized that our chassis had a few too many modifications, namely in the rear, that would make a bolt-on effort more of a challenge than a convenience. We knew we wanted to use stainless steel as the material and we wanted a system that would allow the LS engine to breathe easily if we decided to go with a forced induction system in the future. A full 3-inch system would be great, but there were a few areas where routing that large tubing might prove problematic. That’s when a conversation with our buddy Joey Granatelli lit a spark. It just so happened that his company, Granatelli Motor Sports, offers a line of stainless steel exhaust components, not in round tubing but oval. This ticked both of our boxes on our list of “must-haves” as well as solving our fitment issue when it came to the larger, 3-inch-diameter tubing.
Granatelli Motor Sports’ oval exhaust tubing is manufactured using 304 stainless steel and measures 2.2×3.45 inches in outside diameter. Some quick cocktail napkin math tells us that the area of a 2.5-inch exhaust comes in just under 5 square inches, while the larger 3-inch version comes in at just a tick over 7. Granatelli’s oval tubing specs out at just under 6 square inches, so it’s a great compromise between size and capacity. Being constructed from 304 stainless steel gives Granatelli’s exhaust components greater corrosion resistance thanks to an increase in Chromium and Nickel content. This metallurgical makeup also results in an increase in strength and hardness, resulting in an exhaust system that should be bulletproof and remain looking great for years.
If you’ve ever fabricated a custom exhaust system before, you know how challenging it can be dodging suspension components and keeping the system away from any heat-sensitive objects. Packaging the system where the goals of performance, comfort, and reliability are met can provide a challenge, especially when muffler location is limited to a single space under the truck. Mounted under the cab might result in unwanted drone or harmonics at certain rpm, but with certain suspension setups, like a triangulated four-link or trailing arms, one’s options might be limited. That’s where traditional round tubing has a leg up on oval tubing as it’s a simple matter of rotating a bend slightly to gain a change of multiple directions in multiple planes in one move. Routing with oval tubing only allows for a single change of direction with each bend (horizontal versus vertical). But with its increase in clearance thanks to the lower height that routing challenge comes welcomed. One positive thing that we discovered during the fabrication portion of the exhaust is that keeping things symmetrical with an oval system was actually easier than traditional round tubing for the fact that direction of travel can’t change in more than one plane. A 45-degree bend to the left could be kept perfectly level if both cut surfaces are square and a little attention to detail is maintained.
While providing a welcome challenge, our Granatelli oval exhaust system looked even better than round tubing systems that we’ve done in the past and should give our LS engine plenty of room to breathe.
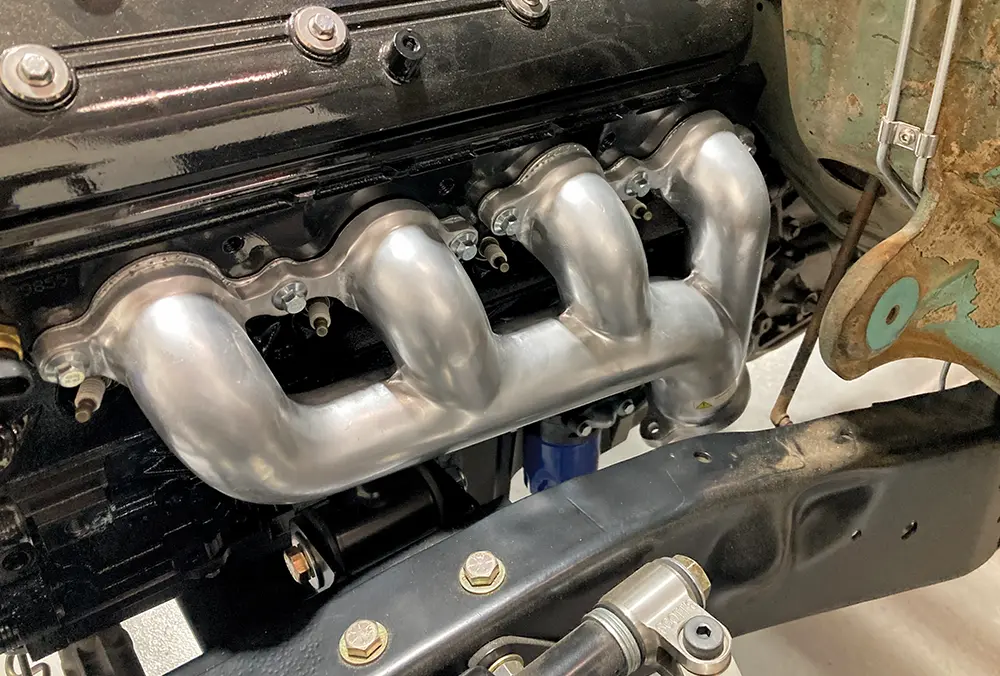
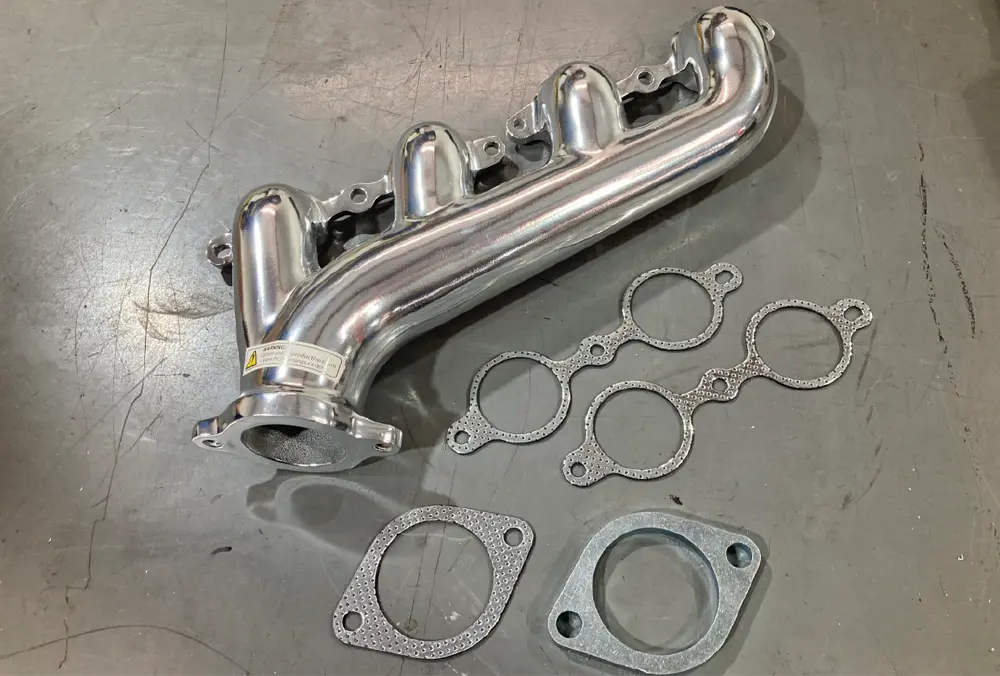
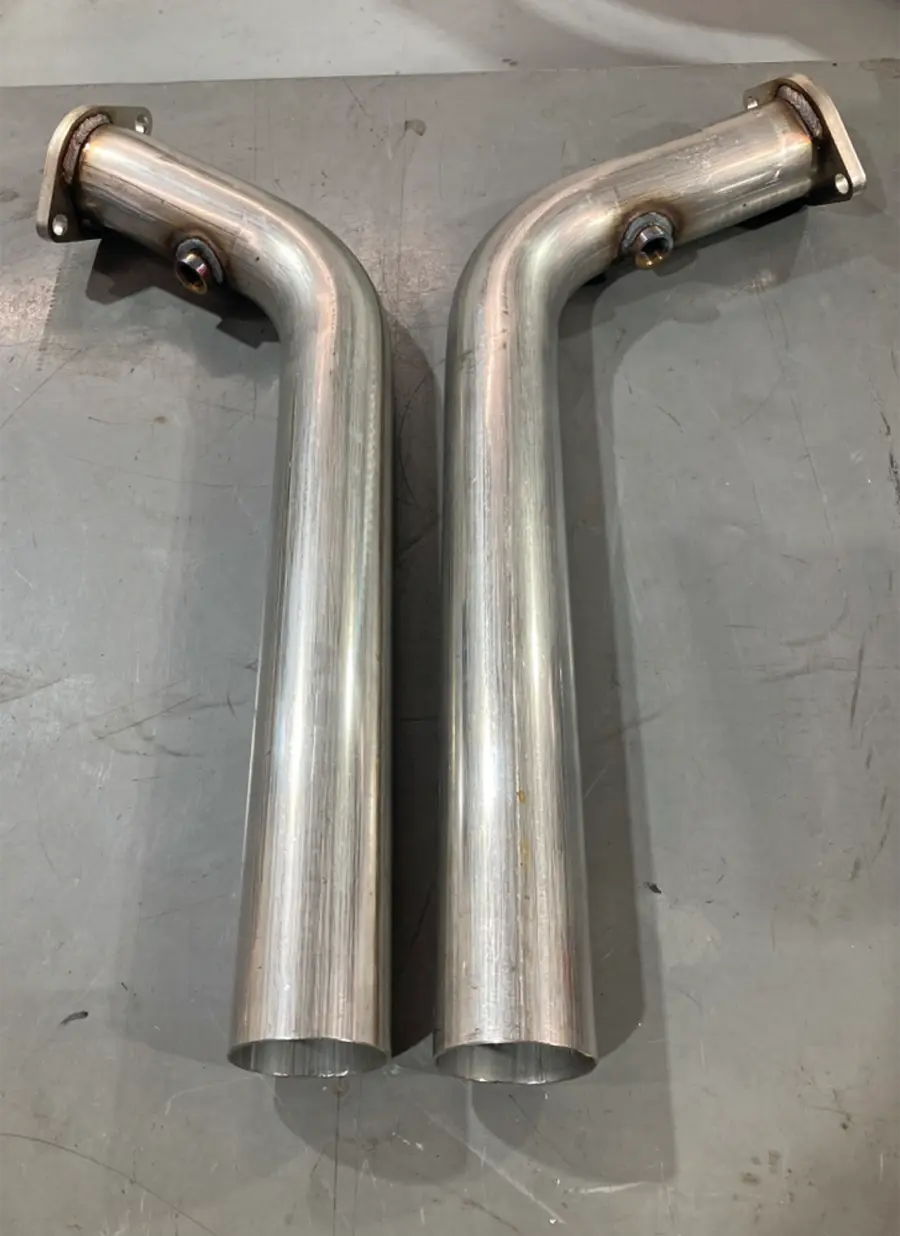
3. To make the transition from our CPP manifolds to the main portion of the exhaust, we’ll be using a pair of Hooker Blackheart Intermediate Pipes (PN HOK-BH13205) from Summit Racing. These 2-1/2-inch stainless steel transitions will set the stage for the rest of the exhaust as it transitions from the manifolds to the straight section.
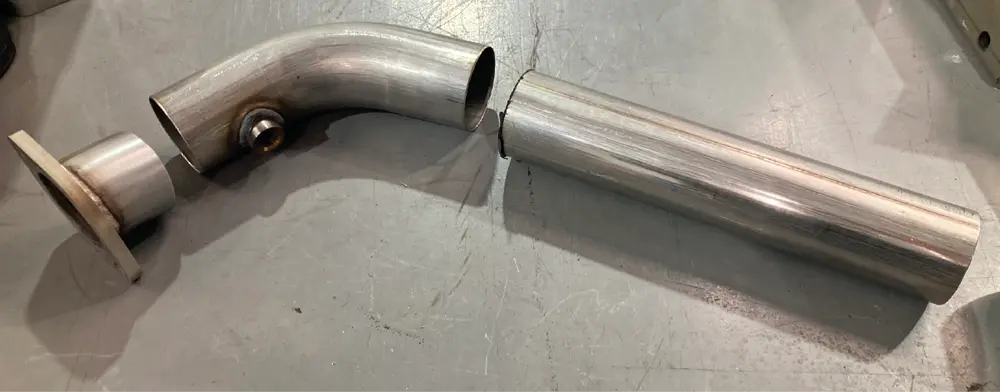


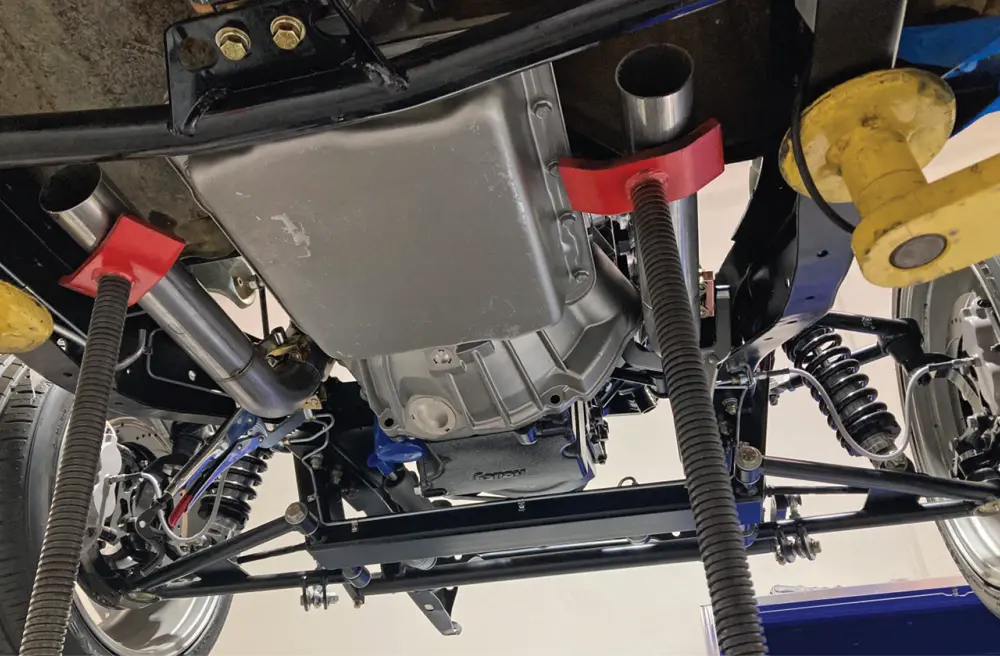

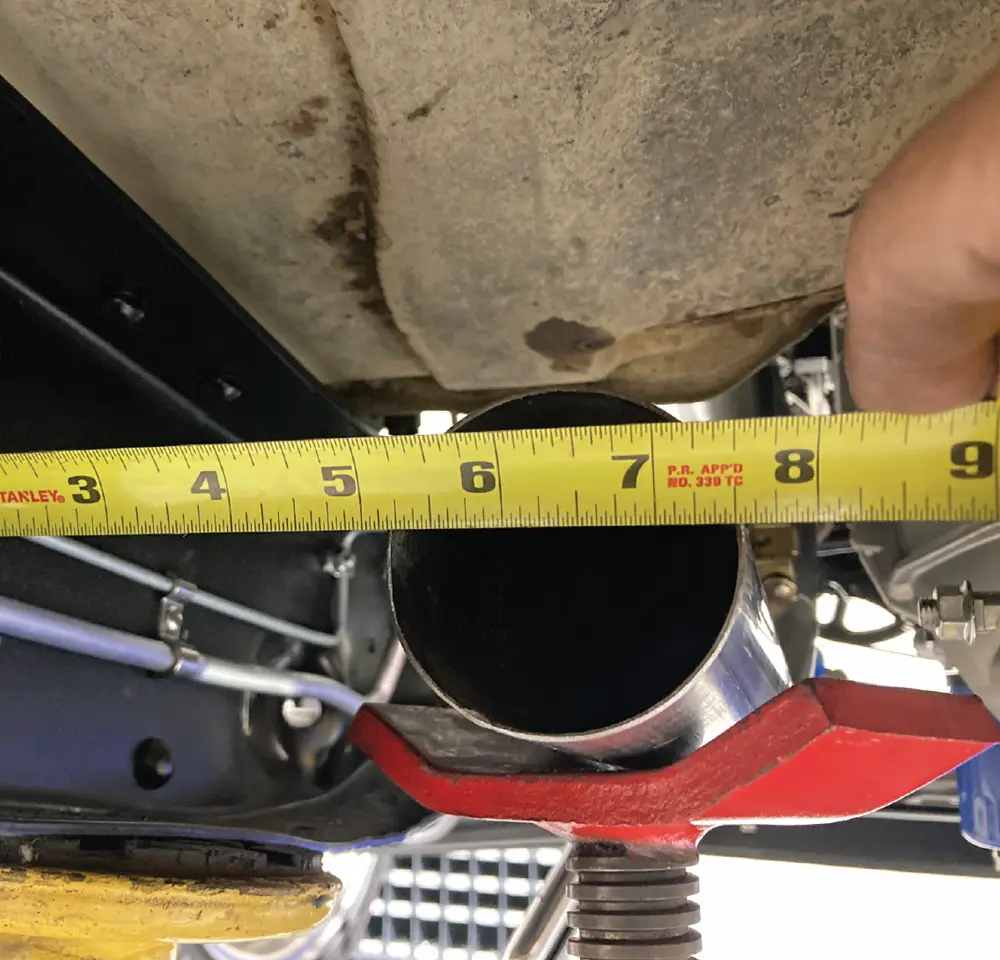
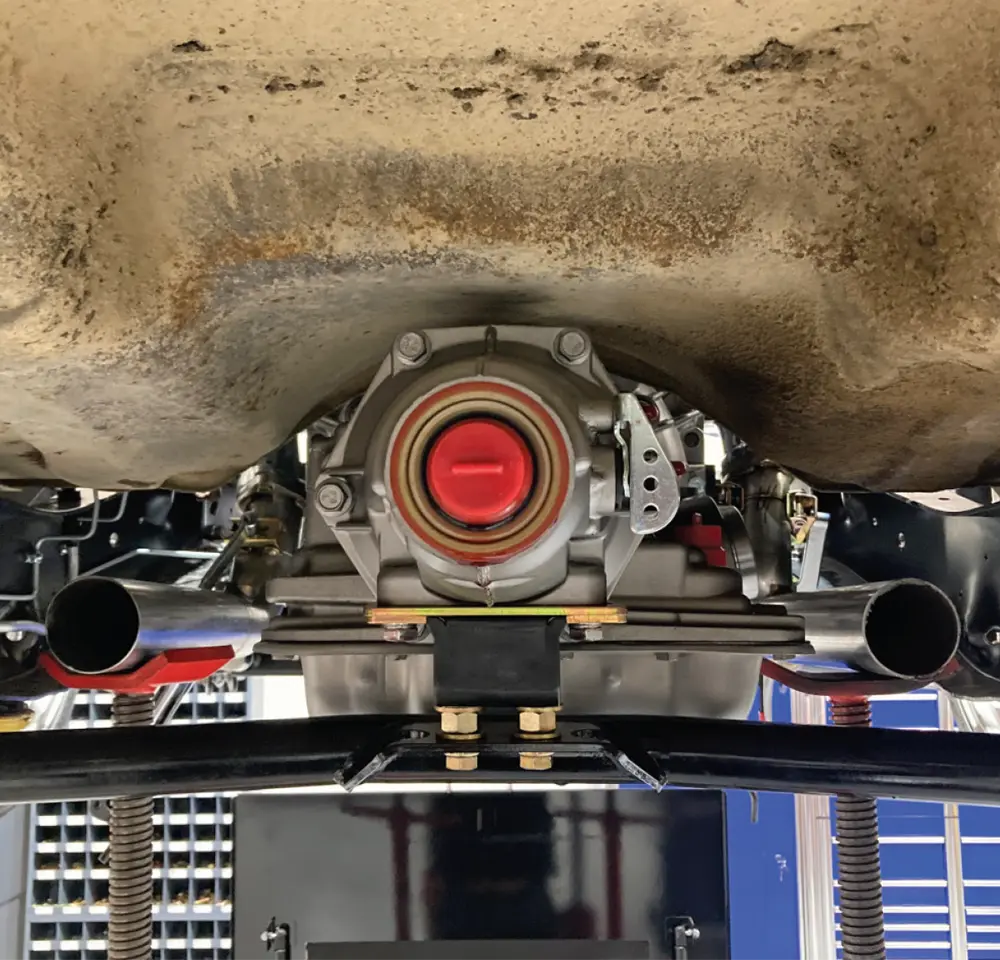
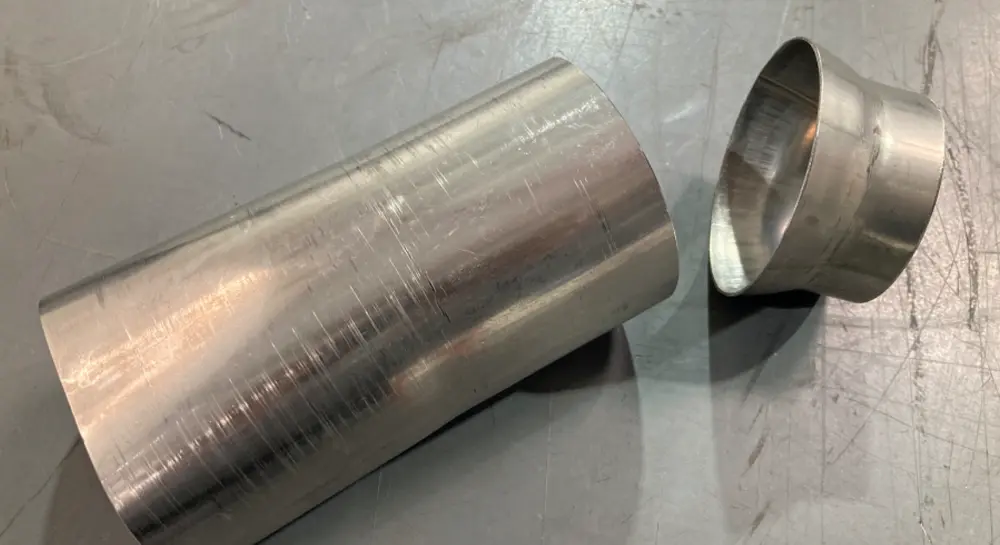
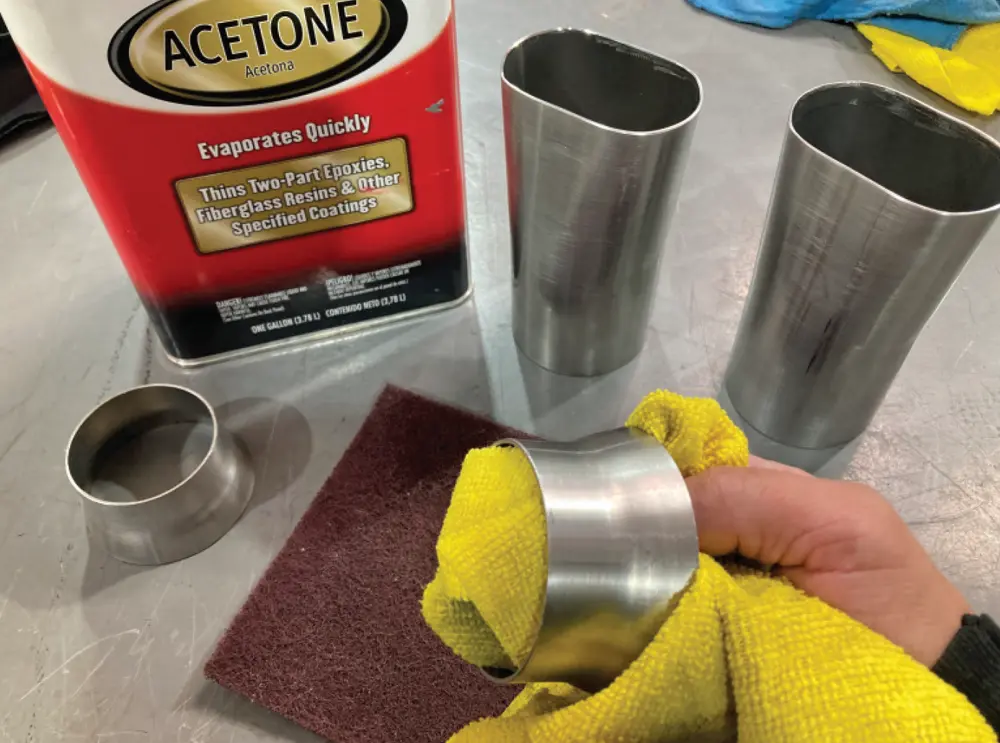
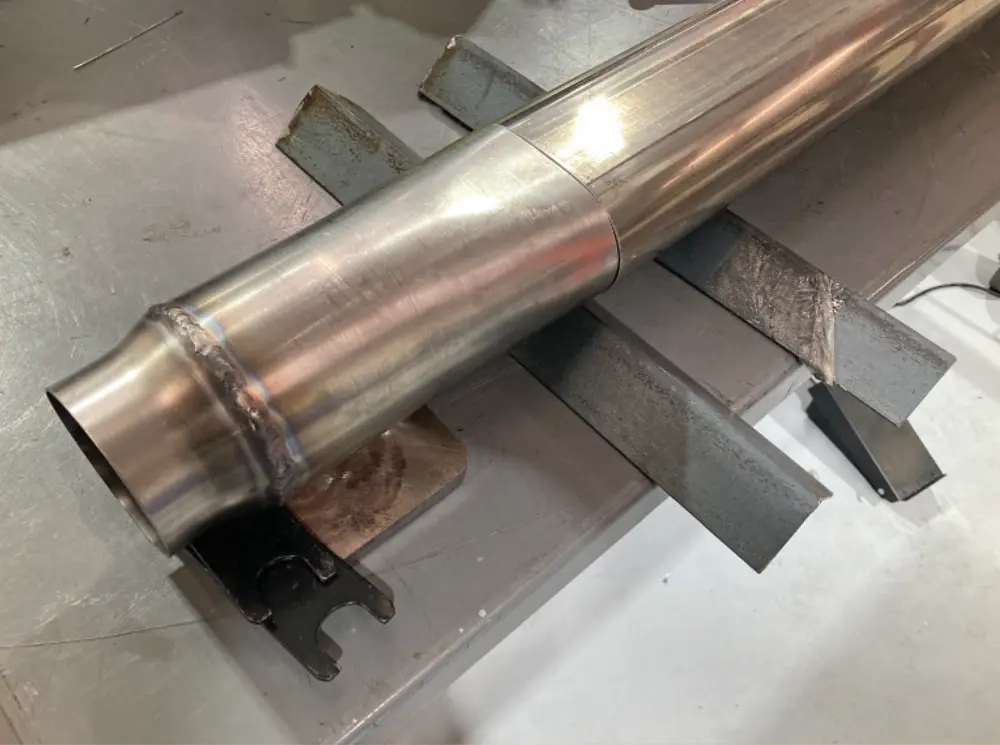
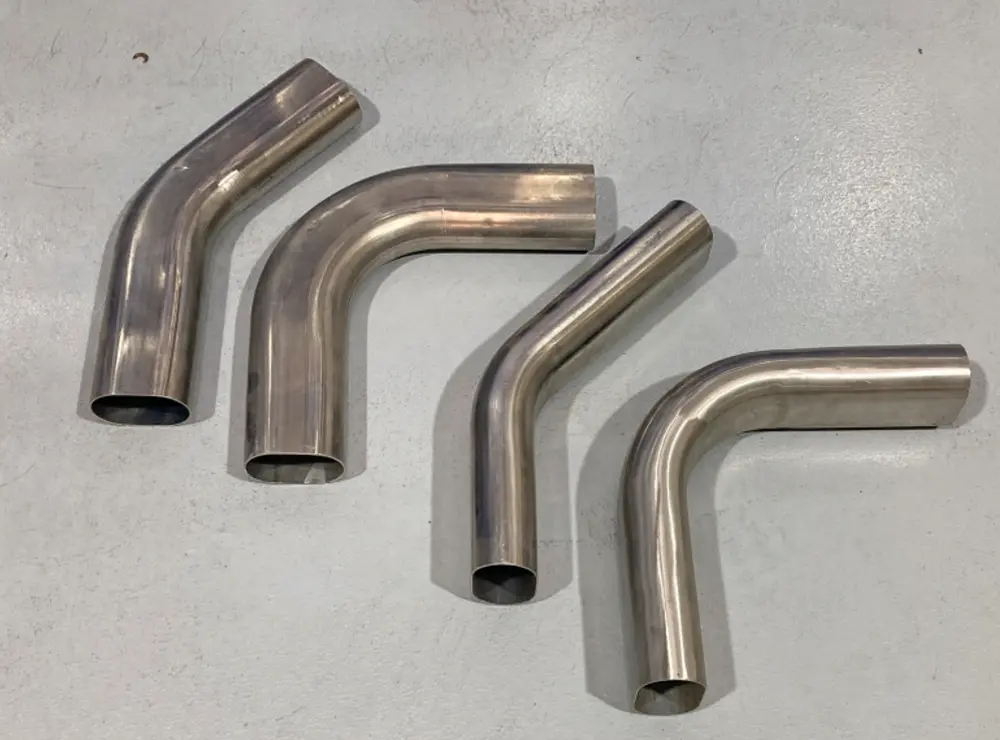
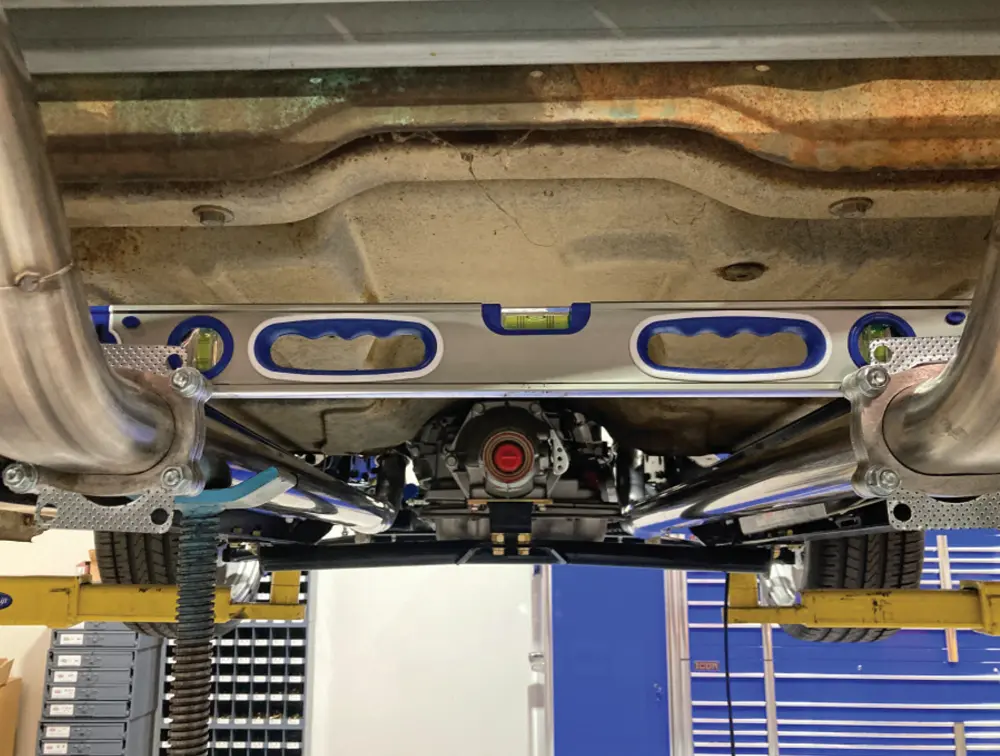
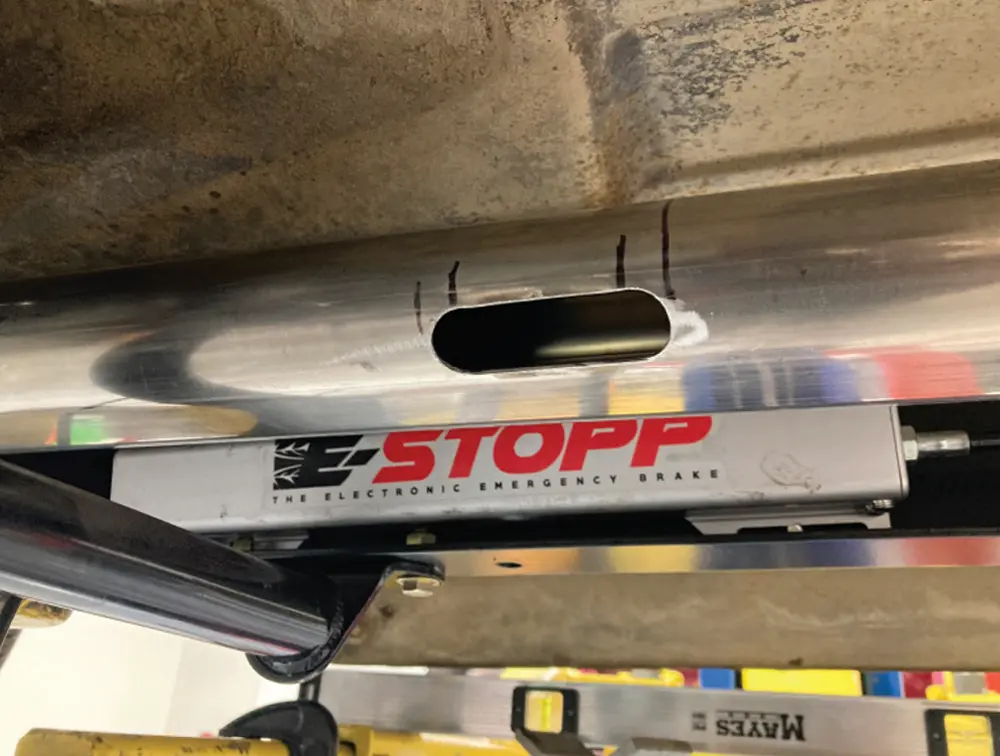
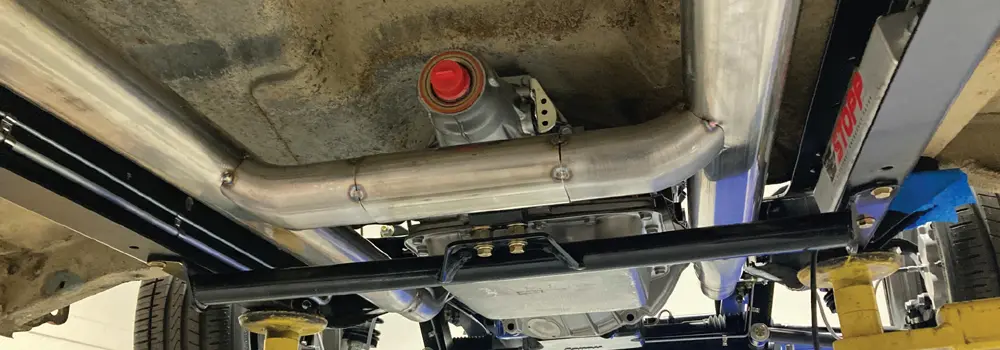
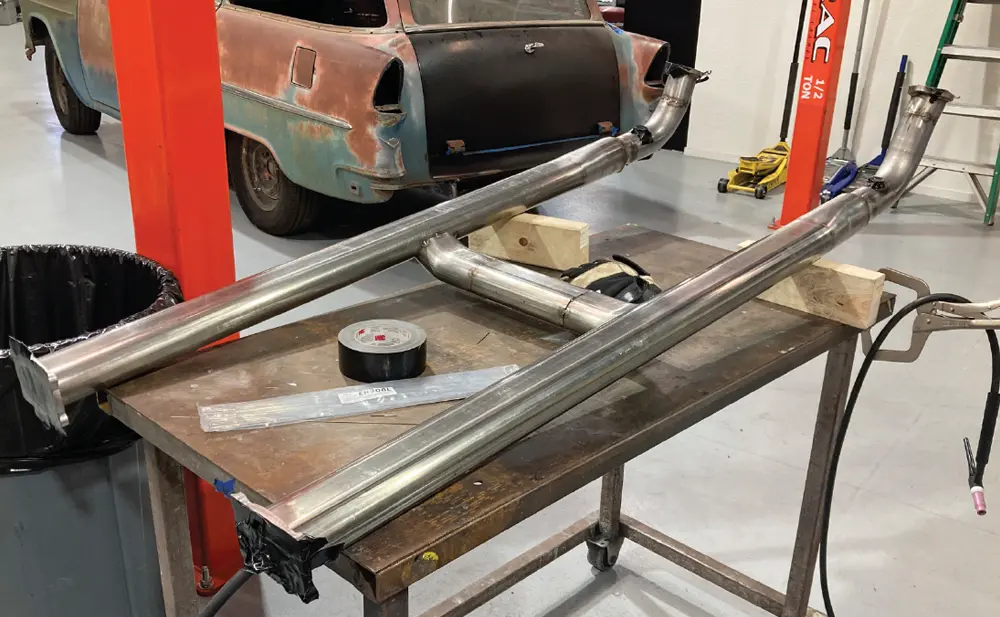

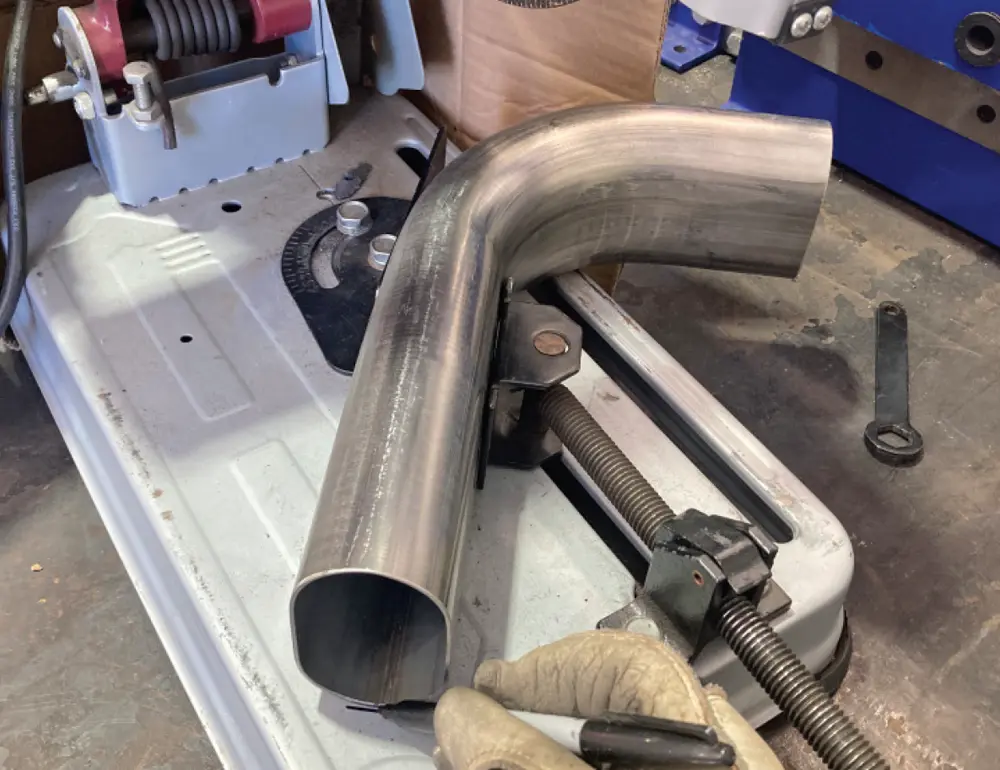

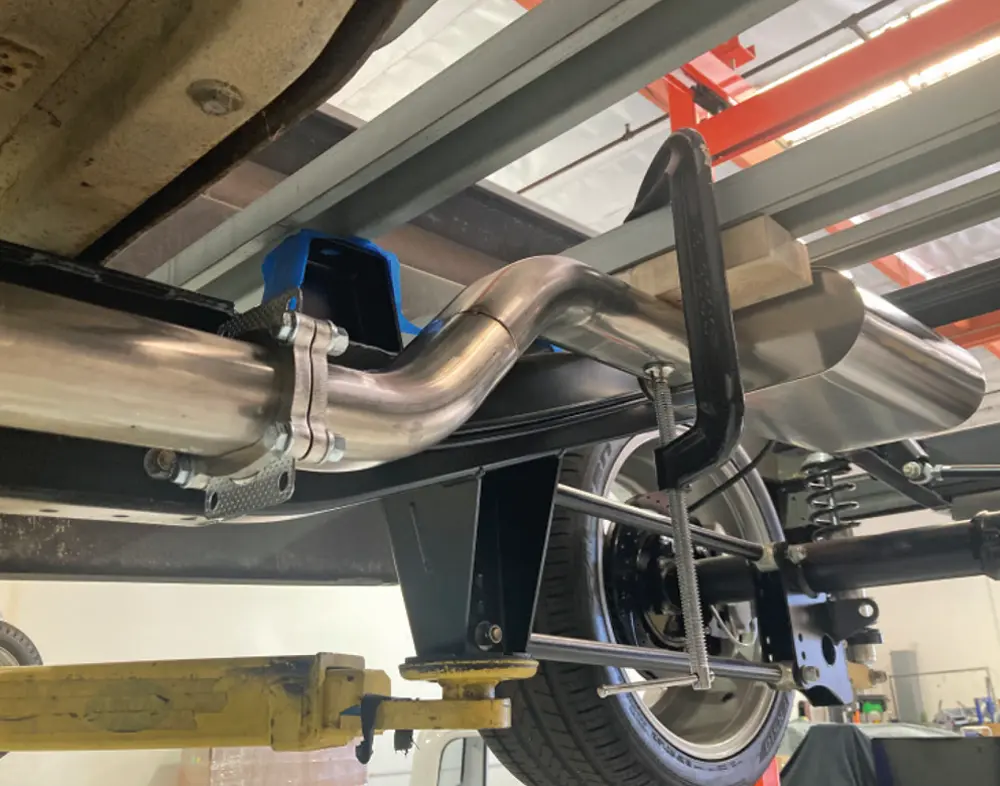

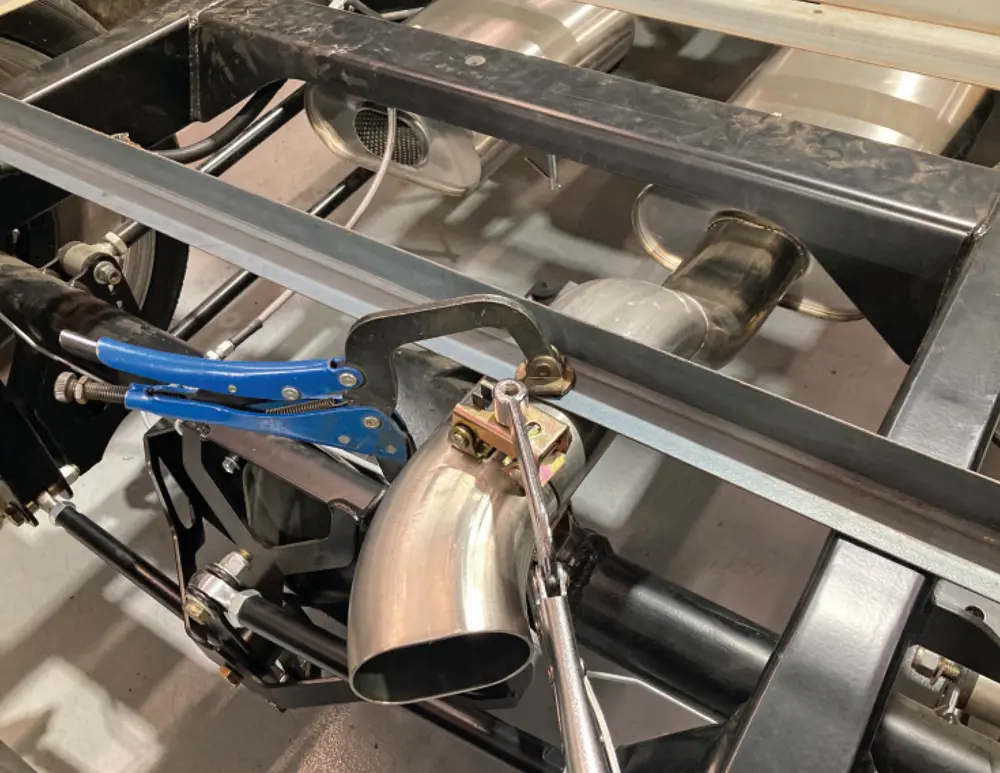
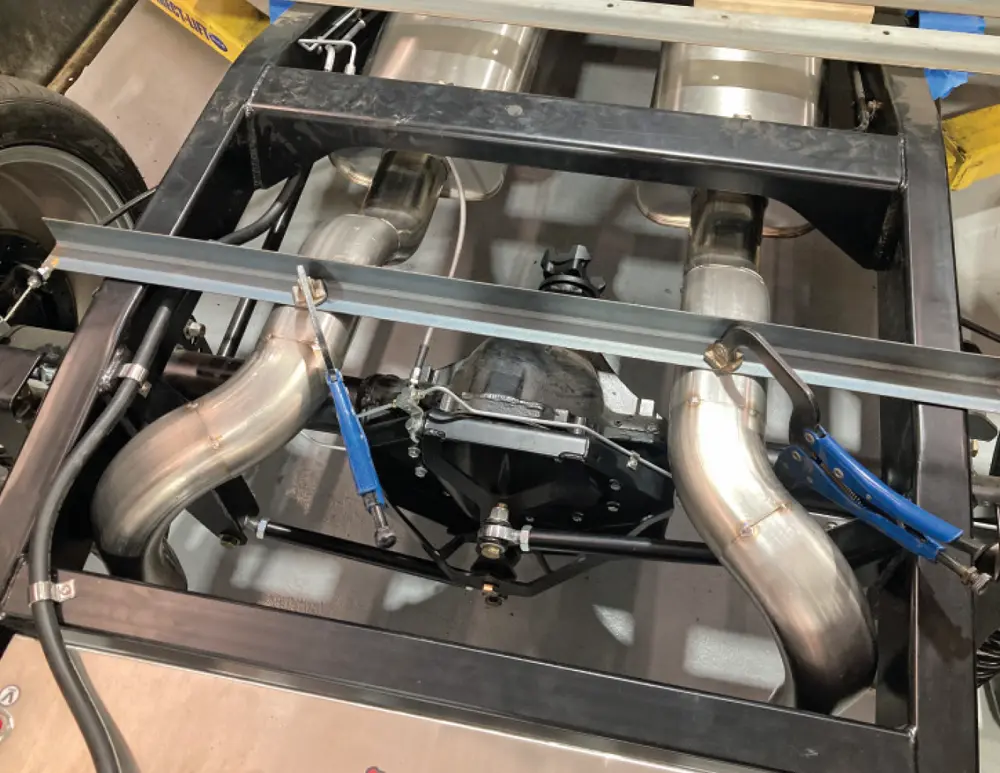

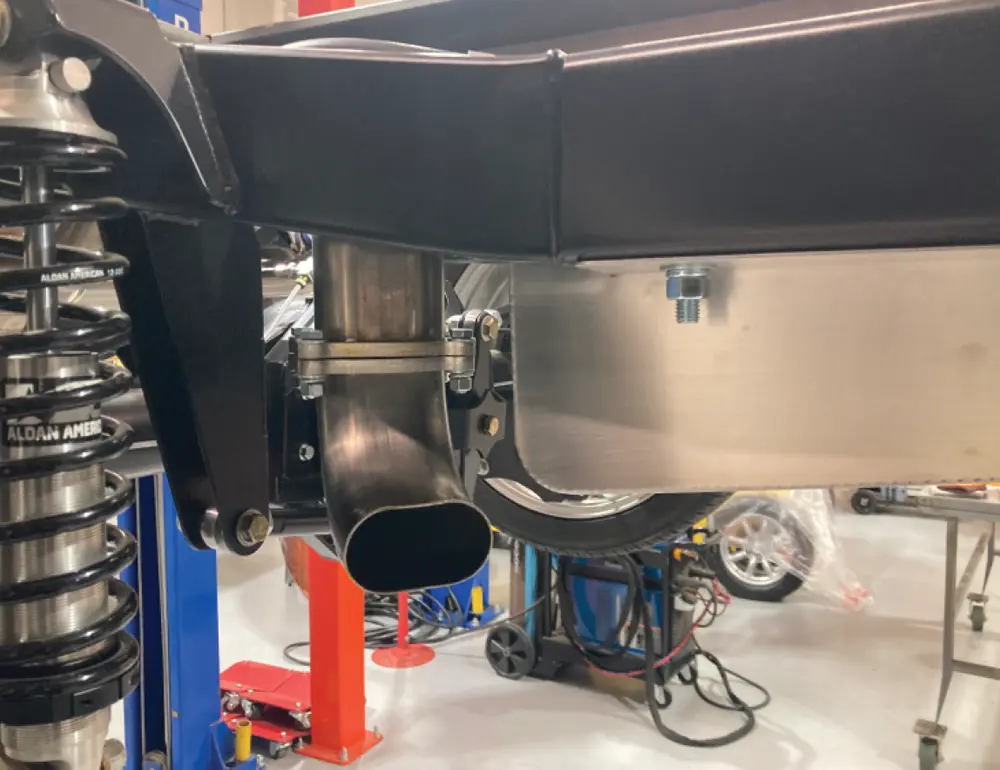


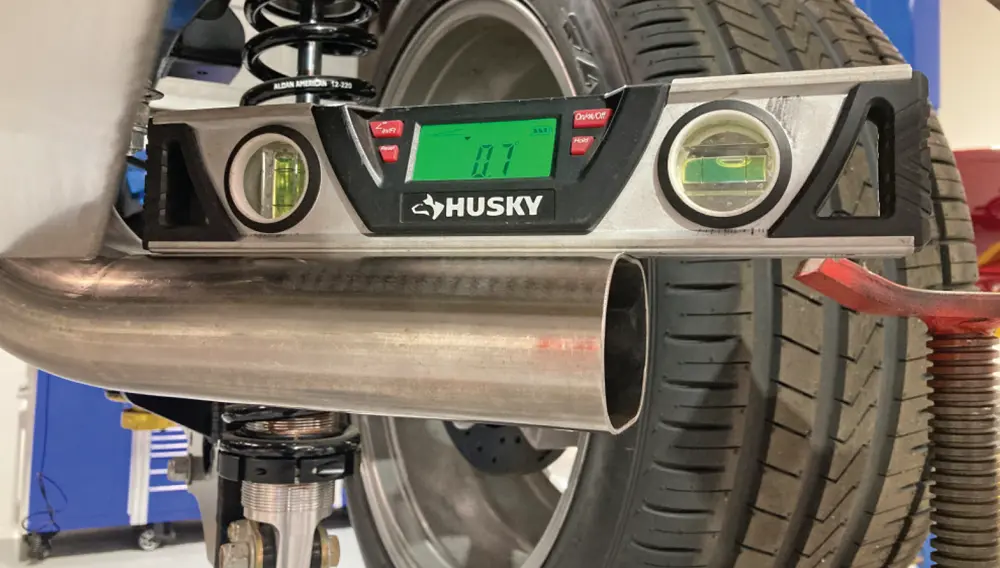

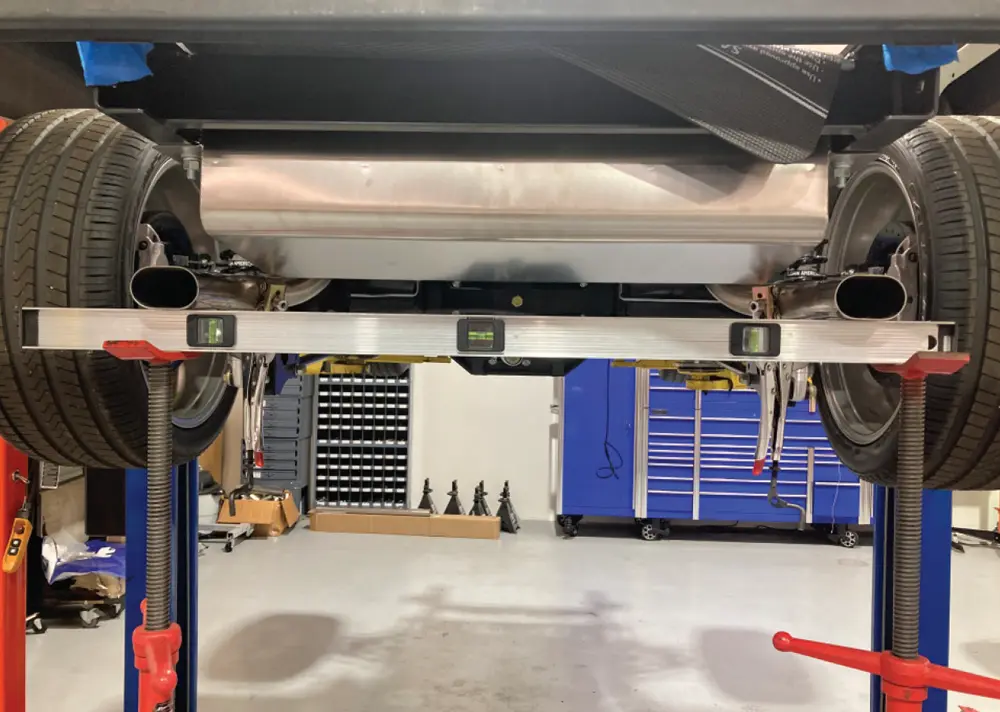


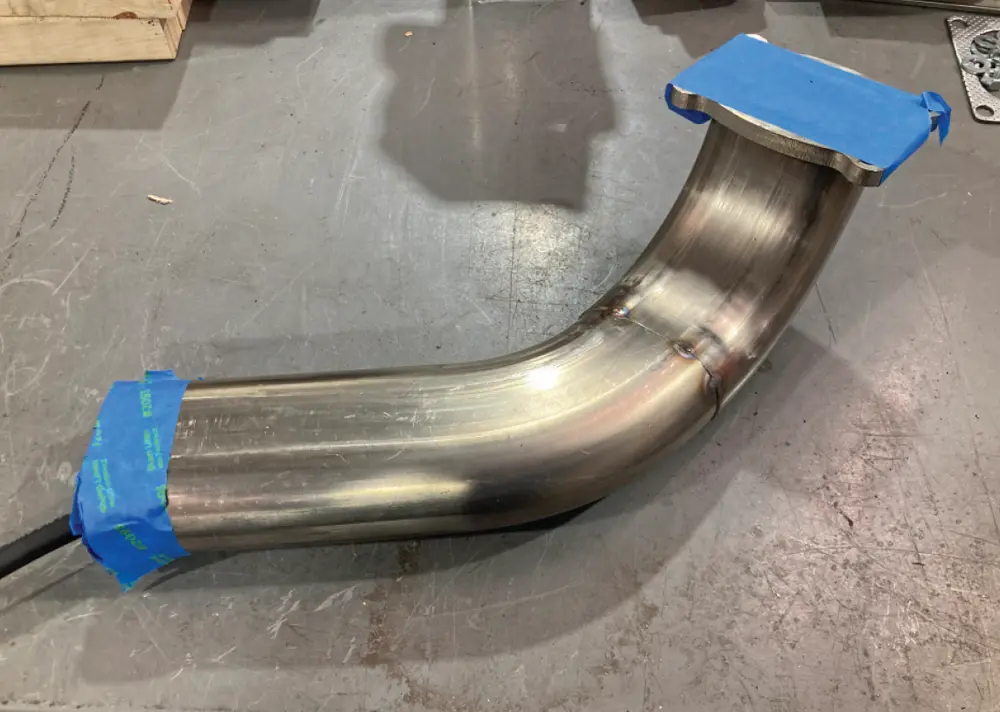
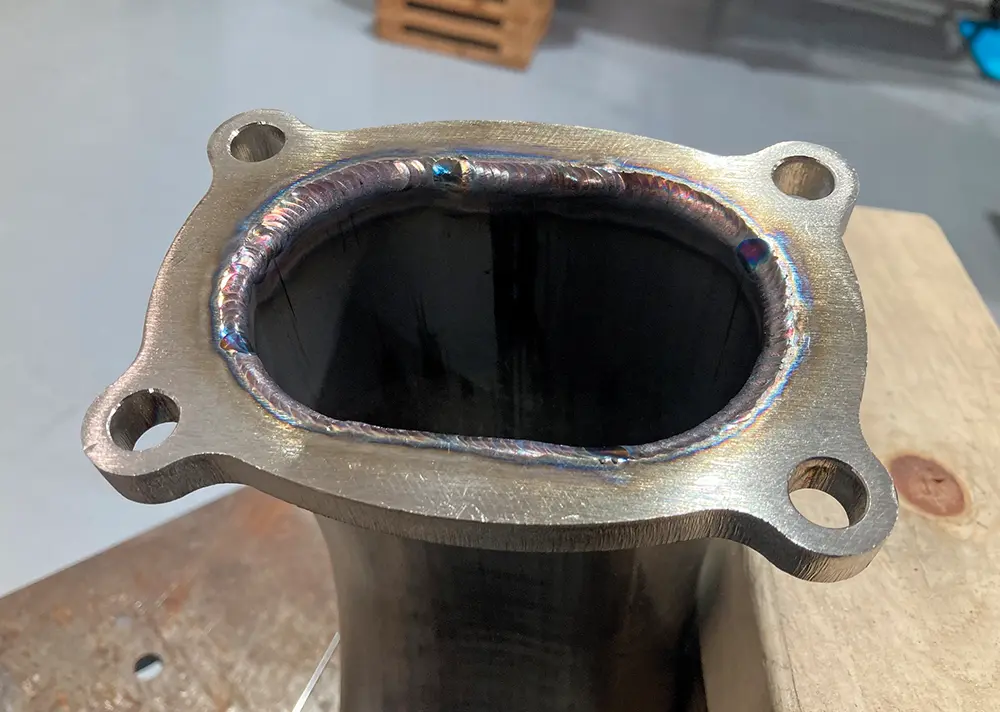
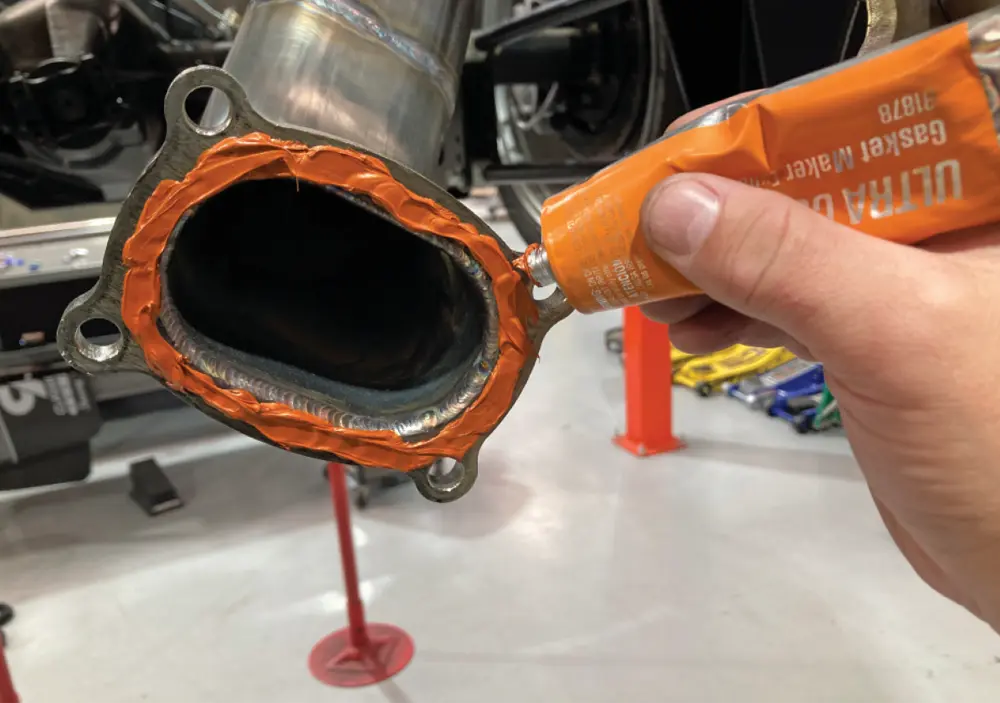
37. High-Temp RTV sealant is applied between the two flanged surfaces to ensure a leak-free assembly.
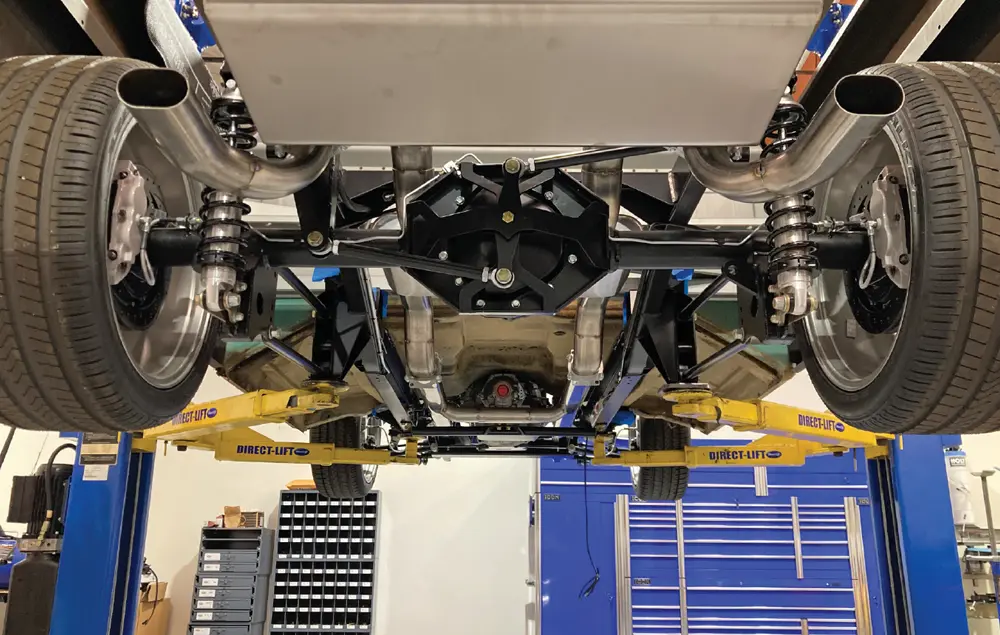
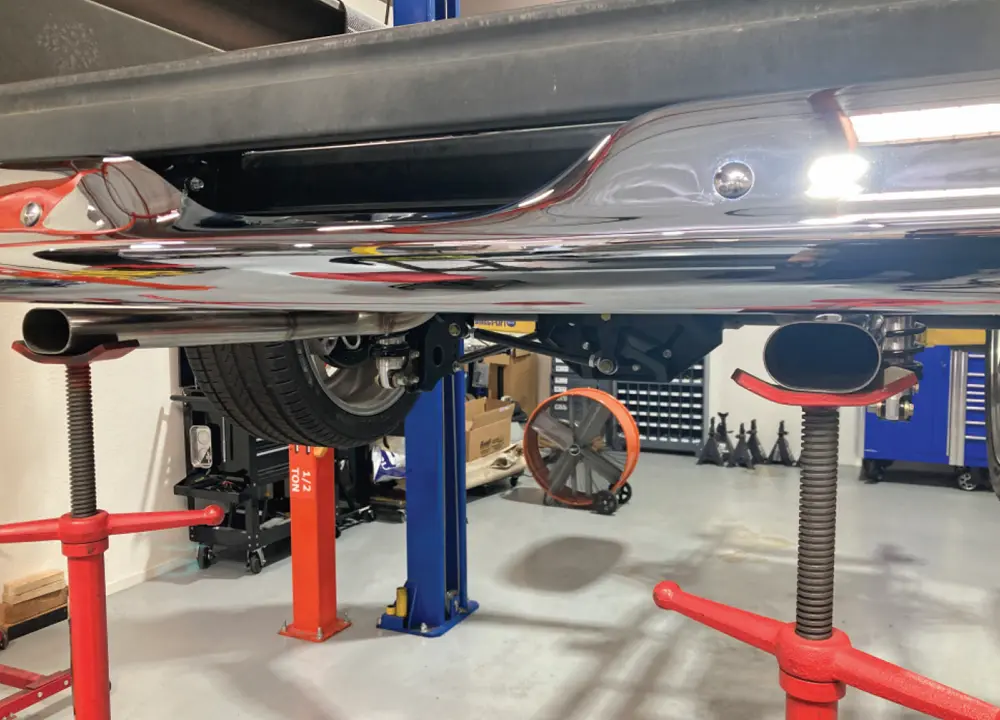
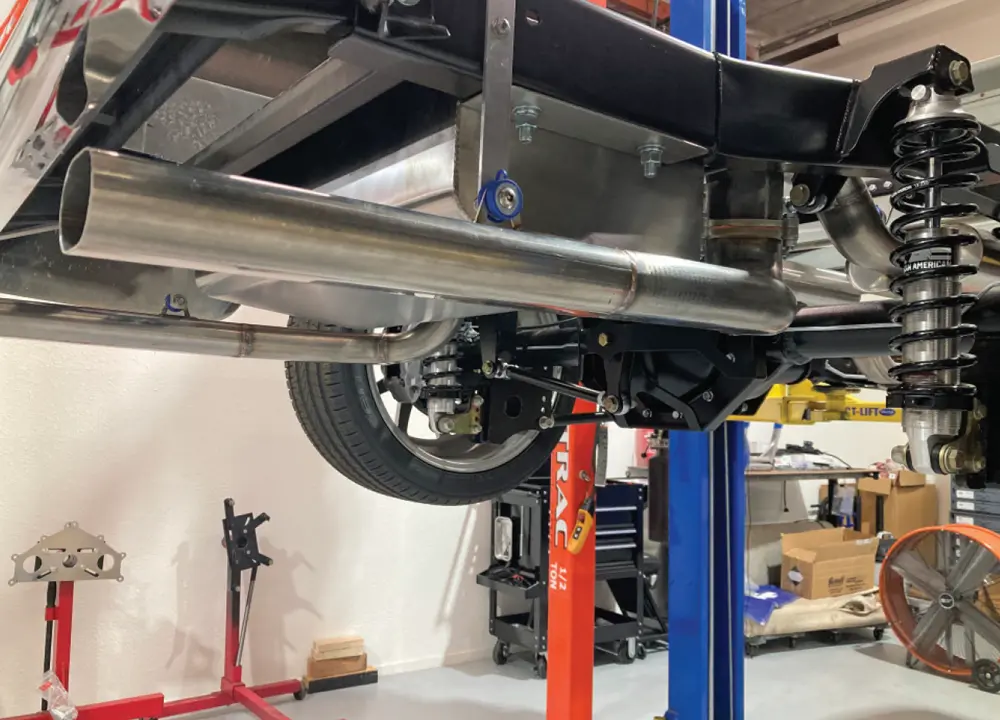
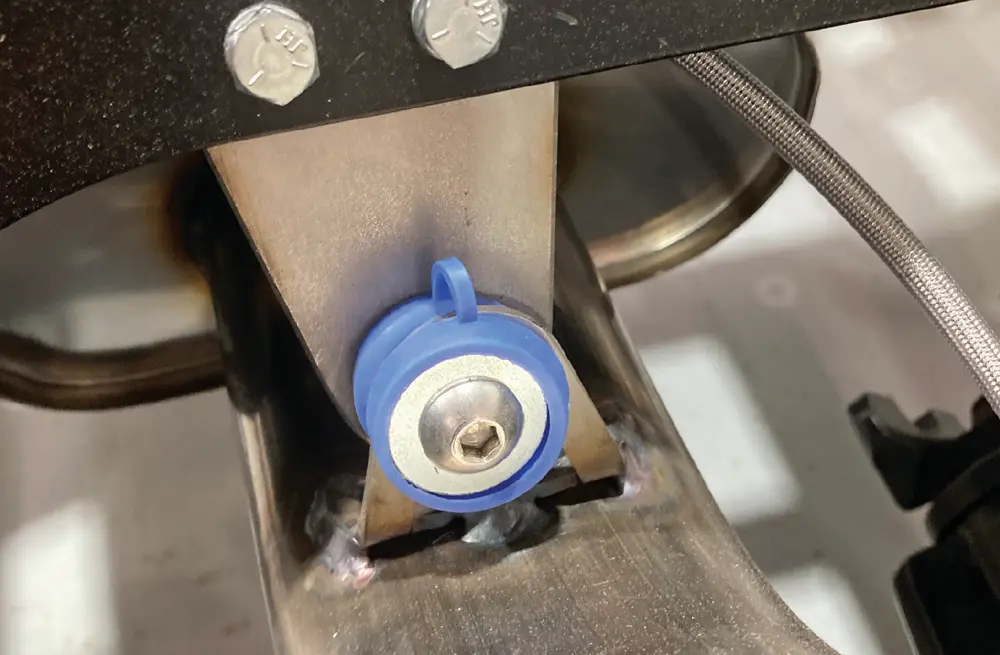
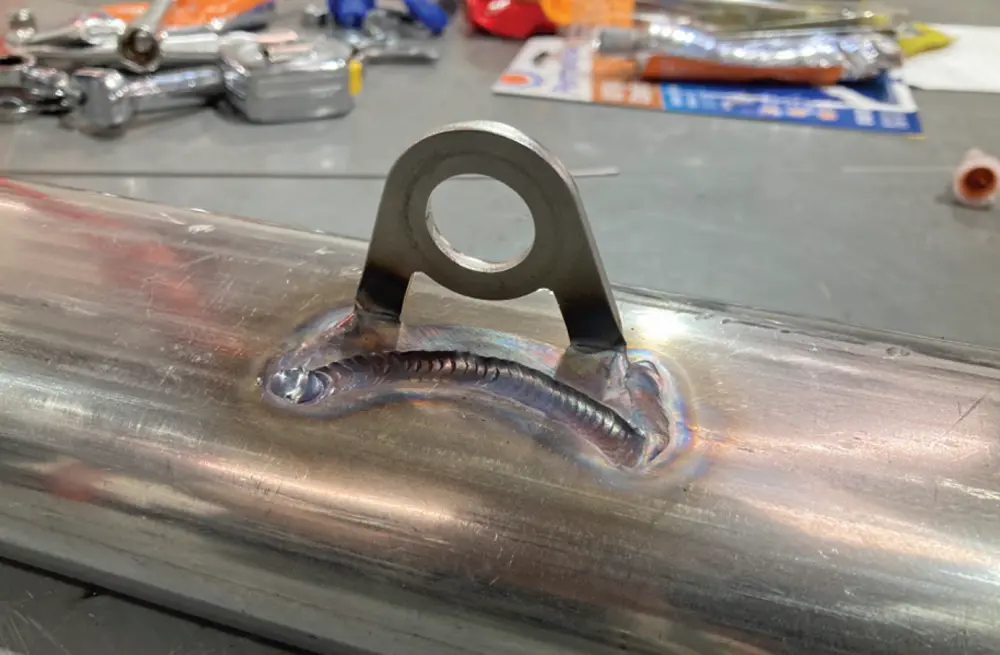
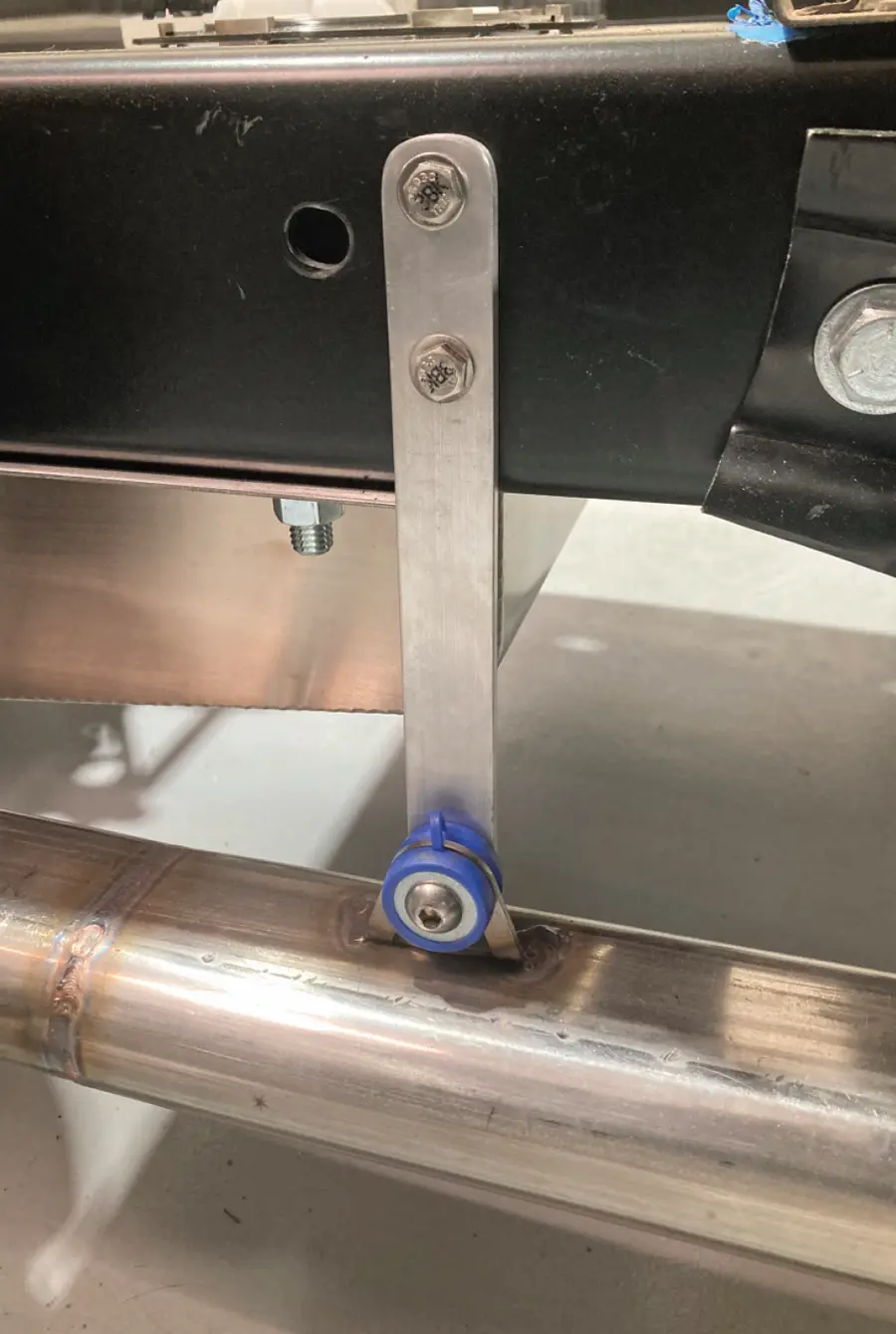
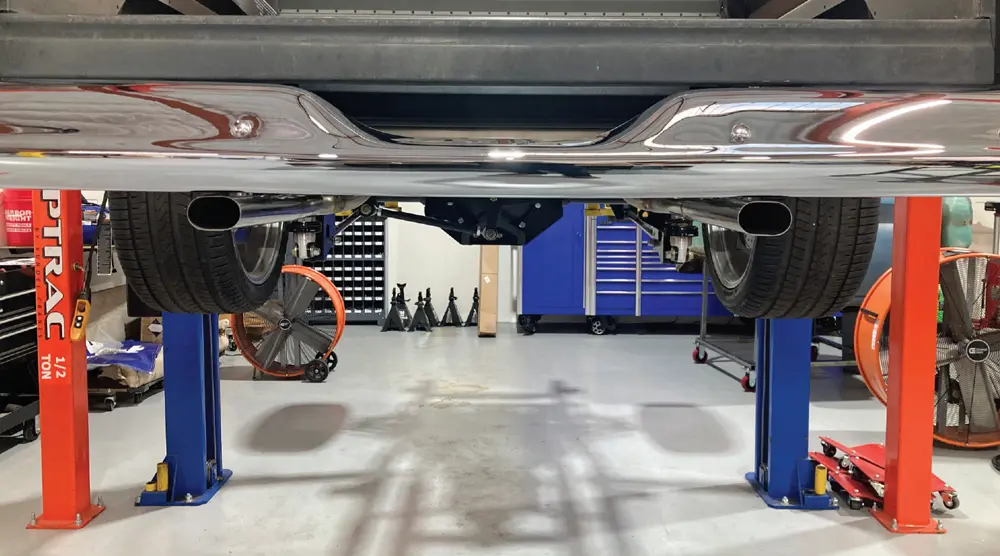
